Glossary
This glossary is available to help you understand important terms related to metals, alloys and metal processing.
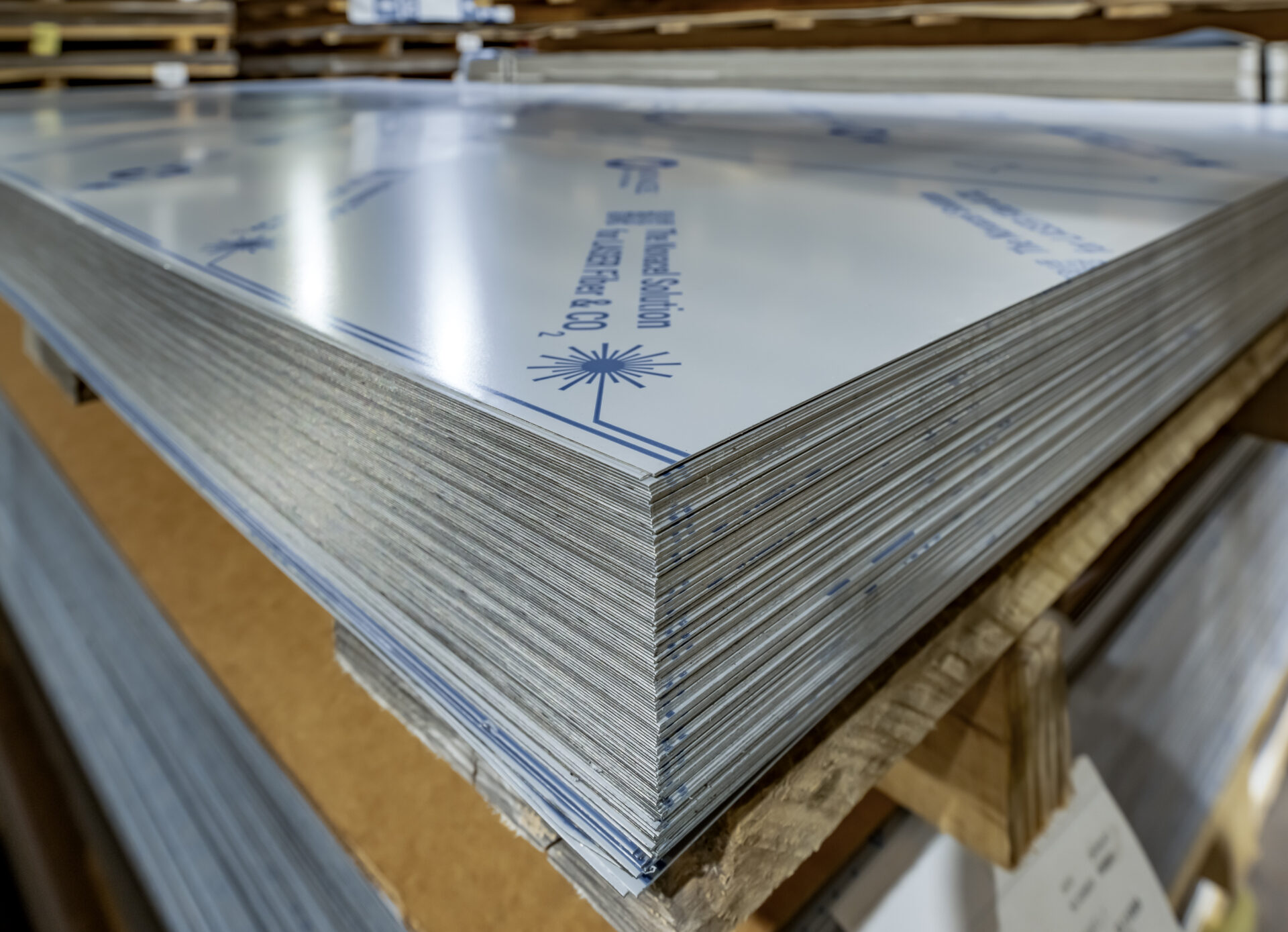
Acid Steel | Steel melted in a furnace that has an acid bottom and lining and under a slag that is dominantly siliceous. | ||||||||||||||||||||||||||||
Aging | Change in a metal by which its structure recovers from an unstable condition produced by quenching or by cold working such as cold reduction. The change in structure is marked by changes in mechanical properties. Aging which takes place slowly at room temperature may be accelerated by slight increase in temperature. See "strain aging". | ||||||||||||||||||||||||||||
Alloy | A substance that has metallic properties and is composed of two or more chemical elements of which at least one is a metal. | ||||||||||||||||||||||||||||
Alloying Element | Chemical elements constituting an alloy; in steels, usually limited to the metallic elements added to modify the properties of the steel. | ||||||||||||||||||||||||||||
Alloy Steel | Steel containing significant quantities of alloying elements (other than carbon and the commonly accepted amounts of manganese, silicon, sulphur and phosphorus) added to effect changes in the mechanical or physical properties. | ||||||||||||||||||||||||||||
Annealing | A process involving heating and cooling, usually applied to induce softening. The term also refers to treatments intended to alter mechanical or physical properties, produce a definite microstructure, or remove gases. When applicable, the following more specific terms should be used: black annealing, blue annealing, box annealing, bright annealing, full annealing, graphitizing, isothermal annealing, malleablizing, process annealing, spheroidizing, stabilizing annealing. Definitions of some of these are given in their alphabetical positions in this glossary. When applied to ferrous alloys, the term "annealing", without qualification, implies full annealing. Any process of annealing will usually reduce stresses, but if the treatment is applied for the sole purpose of such relief, it should be designated as "stress relieving". | ||||||||||||||||||||||||||||
Artificial Aging | An aging treatment above room temperature. | ||||||||||||||||||||||||||||
Austenite | A solid solution in which gamma iron is the solvent; characterized by a face-centered cubic crystal structure. | ||||||||||||||||||||||||||||
Austenitizing | The process of forming austenite by heating a ferrous alloy into the transformation range (partial austenitizing) or above the transformation range (complete austenitizing). | ||||||||||||||||||||||||||||
Basic Oxygen Process | The family of named steelmaking processes in which certain oxidizable constituents in the charge serve as fuel for the melting and refining of the charge. High purity oxygen is injected through a lance against a charge and reacts to physically stir the bath and burn to oxides the carbon, silicon, manganese, and even iron contents to predictable levels, thus creating the heat and refining the steel. Liquid fuels or fluxes may be injected along with the oxygen. | ||||||||||||||||||||||||||||
Basic steel | Steel melted in a furnace that has a basic bottom and lining, and under a slag that is dominantly basic. | ||||||||||||||||||||||||||||
Bend tests | Various tests used to determine the ductility of sheet or plate that is subjected to bending. These tests may include determination of the minimum radius or diameter required to make a satisfactory bend and the number of repeated bends that the material can withstand without failure when it is bent through a given angle and over a definite radius. | ||||||||||||||||||||||||||||
Bessemer Process | A process for making steel by blowing air through molten pig iron contained in a suitable vessel, and thus causing rapid oxidation mainly of silicon and carbon. | ||||||||||||||||||||||||||||
Billet | See bloom. | ||||||||||||||||||||||||||||
Blast Furnace | A shaft furnace in which solid fuel is burned with an air blast to smelt ore in a continuous operation. Where the temperature must be high, as in the production of pig iron, the air is preheated. Where the temperature can be lower, as in smelting copper, lead and tin ores, a smaller furnace is economical, and preheating of the blast is not required. | ||||||||||||||||||||||||||||
Bloom | (slab, billet). Semi-finished products hot rolled from ingots and rectangular in cross section, with rounded corners. The chief differences are in cross-sectional area, in ratio of width to thickness, and in the intended uses. The American Iron and Steel Institute Steel Products Manual Section 2 (1943) classify general usage thus: Min. Width Min. Thickness Cross-Sectional Area
*Generally Blooms, slabs and billets of rerolling quality are intended for hot rolling into common products such as shapes, plates, strip, bars, wire rod, sheet and black plate. Blooms, slabs and billets of forging quality are intended for conversion into forgings or other products to be heat treated. |
||||||||||||||||||||||||||||
Blue brittleness | Reduced ductility occurring as a result of strain aging, when certain ferrous alloys are worked between 150 and 370°C. This phenomenon may be observed at the working temperature or subsequently at lower temperatures. | ||||||||||||||||||||||||||||
Brinell Hardness Test | A test for determining the hardness of a material by forcing a hard steel or carbide ball of specified diameter into it under a specified load. The result is expressed as the Brinell hardness number, which is the value obtained by dividing the applied load in kilograms by the surface area of the resulting impression in square millimeters. | ||||||||||||||||||||||||||||
Brittle Crack Propagation | A very sudden propagation of a crack with the absorption of no energy except that stored elastically in the body. Microscopic examination may reveal some deformation even though it is not noticeable to the unaided eye. | ||||||||||||||||||||||||||||
Brittle Fracture | Fracture with little or no plastic deformation. | ||||||||||||||||||||||||||||
Brittleness | A tendency to fracture without appreciable deformation. | ||||||||||||||||||||||||||||
Burnt | A term applied to a metal permanently damaged by having been heated to a temperature close to the melting point. | ||||||||||||||||||||||||||||
Camber | Curvature in the plane of rolled sheet or strip, or in the plane of the web of structural shapes. | ||||||||||||||||||||||||||||
Capped Steel | Semi-killed steel cast in a bottle-top mold and covered with a cap fitting into the neck of the mold. The cap causes the top metal to solidify. Pressure is built up in the sealed- in molten metal and results in a surface condition much like that of rimmed steel. | ||||||||||||||||||||||||||||
Carbide | A compound of carbon with one or more metallic elements. | ||||||||||||||||||||||||||||
Carbon Steel | Steel that owes its properties chiefly to the presence of carbon, without substantial amounts of other alloying elements; also termed "ordinary steel", "straight carbon steel", "plain carbon steel". | ||||||||||||||||||||||||||||
Carburizing | A process that introduces carbon into a solid ferrous alloy by heating the metal in contact with a carbonaceous material-solid, liquid or gas-to a temperature above the transformation range and holding at that temperature. | ||||||||||||||||||||||||||||
Cast Iron | Carburizing is generally followed by quenching to produce a hardened case. An iron containing carbon in excess of the solubility in the austenite that exists in the alloy at the eutectic temperature. | ||||||||||||||||||||||||||||
Cast Steel | Any object made by pouring molten steel into moulds. | ||||||||||||||||||||||||||||
Cementite | A compound of iron and carbon known as "iron carbide" which has the approximate chemical formula Fe3C and is characterized by an orthorhombic crystal structure. | ||||||||||||||||||||||||||||
Charge | (1) The liquid and solid materials fed into a furnace for its operation. (2) Weights of various liquid and solid materials put into a furnace during one feeding cycle. | ||||||||||||||||||||||||||||
Charpy Test | A pendulum type single-blow impact test in which the specimen, usually notched, is supported at both ends as a simple beam and broken by a falling pendulum. The energy absorbed, as determined by the subsequent rise of the pendulum, is a measure of impact strength or notch toughness. | ||||||||||||||||||||||||||||
Check Analysis | Chemical analysis made of drillings taken from semi-finished or finished products. The units are subject to certain specified variations from the ladle analysis. | ||||||||||||||||||||||||||||
Chipping | A method for removing seams and other surface defects with chisel or gouge so that such defects will not be worked into the finished product. Chipping is often employed also to remove metal that is excessive but not defective. Removal of defects by gas cutting is known as "de-seaming" or "scarfing". | ||||||||||||||||||||||||||||
Cluster Mill | A rolling mill where each of the two working rolls of small diameter is supported by two or more backup rolls. | ||||||||||||||||||||||||||||
Cold Work | Plastic deformation at such temperatures and rates that substantial increases occur in the strength and hardness of the metal. Visible structural changes include changes in grain shape and, in some instances, mechanical twinning or banding. | ||||||||||||||||||||||||||||
Cold Working | Deforming a metal plastically at such a temperature and rate that strain hardening occurs. The upper limit of temperature for this process is the recrystallization temperature. | ||||||||||||||||||||||||||||
Compressive Strength | Yield the maximum stress that a metal, subjected to compression, can withstand without a predefined amount of deformation. Ultimate-The maximum stress that a brittle material can withstand without fracture when subjected to compression. | ||||||||||||||||||||||||||||
Continuous Casting | A casting technique in which an ingot, billet, tube or other shape is continuously solidified while it is being poured, so that its length is not determined by mold dimensions. | ||||||||||||||||||||||||||||
Continuous Mill | A rolling mill consisting of a number of stands of synchronized rolls (in tandem) in which metal undergoes successive reductions as it passes through the various stands. | ||||||||||||||||||||||||||||
Controlled Cooling | A process of cooling from an elevated temperature in a predetermined manner, to avoid hardening, cracking or internal damage, or to produce a desired microstructure. This cooling usually follows the final hot forming operation. | ||||||||||||||||||||||||||||
Cooling Stresses | Stresses developed by uneven contraction or external constraint of metal during cooling; also those stresses resulting from localized plastic deformation during cooling, and retained. | ||||||||||||||||||||||||||||
Corrosion | Gradual chemical or electrochemical attack on a metal by atmosphere, moisture, or other agents. | ||||||||||||||||||||||||||||
Creep | The flow or plastic deformation of metals held for long periods of time at stresses lower than the normal yield strength. The effect is particularly important if the temperature of stressing is in the vicinity of the recrystallization temperature of the metal. | ||||||||||||||||||||||||||||
Creep limit | (1) The maximum stress that will cause less than a specified quantity of creep in a given time. (2) The maximum nominal stress under which the creep strain rate decreases continuously with time under constant load and at constant temperature. Sometimes used synonymously with creep strength. | ||||||||||||||||||||||||||||
Creep Strength | (1) The constant nominal stress that will cause a specified quantity of creep in a given time at constant temperature. (2) The constant nominal stress that will cause a specified creep rate at constant temperature. | ||||||||||||||||||||||||||||
Critical Cooling Rate | The minimum rate of continuous cooling just sufficient to prevent undesired transformations. For steel, the slowest rate at which it can be cooled from above the upper critical temperature to prevent the decomposition of austenite at any temperature above the temperature at which the transformation of austenite to martensite starts during cooling. | ||||||||||||||||||||||||||||
Crop | The end or ends of an ingot that contain the pipe or other defects to be cut off and discarded; also termed "crop end" and "discard". | ||||||||||||||||||||||||||||
Cross-Country Mill | A rolling mill in which the mill stands are so arranged that their tables are parallel with a transfer (or cross-over) table connecting them. They are used for rolling structural shapes, rails and any special form of bar stock not rolled in the ordinary bar mill. | ||||||||||||||||||||||||||||
Cross Rolling | The rolling of sheet so that the direction of rolling is changed about 90° from the direction of the previous rolling. | ||||||||||||||||||||||||||||
Crown | In the center of metal sheet or strip, thickness greater than at the edge. | ||||||||||||||||||||||||||||
Crystal | A physically homogeneous solid in which the atoms, ions or molecules are arranged in a three-dimensional repetitive pattern. | ||||||||||||||||||||||||||||
Crystallization | The formation of crystals by the atoms assuming definite positions in a crystal lattice. This is what happens when a liquid metal solidifies. (Fatigue, the failure of metals under repeated stresses, is sometimes falsely attributed to crystallization). | ||||||||||||||||||||||||||||
Cup Fracture (cup and cone fracture) Defect | Fracture, frequently seen in tensile test pieces of a ductile material, in which the surface of failure on one portion shows a central flat area of failure in tension, with an exterior extended rim of failure in shear. Internal or external flaw or blemish. Harmful defects can render material unsuitable for specific end use. | ||||||||||||||||||||||||||||
Deoxidation | Elimination of oxygen in liquid steel, usually by introduction of aluminum or silicon or other suitable element. This term is also used to denote reduction of surface scale (iron oxide). | ||||||||||||||||||||||||||||
Directional Properties | Anisotropic condition where physical and mechanical properties vary, depending on the relation of the test axis to a specific direction of the metal; a result of preferred orientation or of fibering of inclusions during the working. | ||||||||||||||||||||||||||||
Ductility | The property that permits permanent deformation before fracture by stress in tension. | ||||||||||||||||||||||||||||
Elastic Limit | The maximum stress that a material will withstand without permanent deformation. (Almost never determined experimentally; yield strength is customarily determined.) | ||||||||||||||||||||||||||||
Electric Furnace | A melting furnace with a shallow hearth and a low roof in which the charge is melted and refined by an electric arc between one or more electrodes and the charged material. The electrodes normally are suspended through the roof. No liquid or gaseous fuel is usually used; however, gaseous oxygen may be injected into the bath. | ||||||||||||||||||||||||||||
Elongation | The amount of permanent extension in the vicinity of the fracture in the tension test; usually expressed as a percentage of the original gauge length, as 25% in 50 mm. Elongation may also refer to the amount of extension at any stage in any process that elongates a body continuously, as in rolling. | ||||||||||||||||||||||||||||
Embossing | Raising a design in relief against a surface. | ||||||||||||||||||||||||||||
Embrittlement | Reduction in the normal ductility of a metal due to a physical or chemical change. | ||||||||||||||||||||||||||||
Endurance Limit | The maximum stress that a metal will withstand without failure during a specified large number of cycles of stress. If the term is employed without qualification, the cycles of stress are usually such as to produce complete reversal of flexural stress. | ||||||||||||||||||||||||||||
Extrusion | Conversion of a billet into lengths of uniform cross-section by forcing the plastic metal through a die orifice of the desired cross-sectional outline. In "direct extrusion", the die and ram are at opposite ends of the billet, and the product and ram travel in the same direction. In "indirect extrusion" (rare) the die is at the ram end of the billet and the product travels through and in the opposite direction to the hollow ram. A "stepped extrusion" is a single product with one or more abrupt cross-section changes and is obtained by interrupting the extrusion by die changes. "Impact extrusion" (cold extrusion) is the process or resultant product of a punch striking an unheated slug in a confining die. The metal flow may be either between the punch and die or through another opening. "Hot extrusion" is similar to cold extrusion except that a preheated slug is used and the pressure application is slower. | ||||||||||||||||||||||||||||
Fatigue | The tendency for a metal to break under conditions of repeated cyclic stressing considerably below the ultimate tensile strength. | ||||||||||||||||||||||||||||
Fatigue Crack or Failure | A fracture starting from a nucleus where there is an abnormal concentration of cyclic stress and propagating through the metal. The surface is smooth and frequently shows concentric (sea shell) markings with a nucleus as a center. | ||||||||||||||||||||||||||||
Fatigue Life | The number of cycles of stress that can be sustained prior to failure for a stated test condition. | ||||||||||||||||||||||||||||
Fatigue Limit | The maximum stress that a metal will withstand without failure for a specified large number of cycles of stress. Usually synonymous with endurance limit. | ||||||||||||||||||||||||||||
Fatigue Ratio | The ratio of the fatigue limit for cycles of reversed flexural stress to the tensile strength. | ||||||||||||||||||||||||||||
Fatigue Strength | The maximum stress that can be sustained for a specified number of cycles without failure, the stress being completely reversed within each cycle unless otherwise stated. | ||||||||||||||||||||||||||||
Ferrite | A solid solution in which alpha iron is the solvent, and which is characterized by a body-centered cubic crystal structure. | ||||||||||||||||||||||||||||
Finished Steel | Steel that is ready for the market without further work or treatment. Blooms, billets, slabs, sheet bars, and wire rods are termed “semi-finished". | ||||||||||||||||||||||||||||
Finishing Temperature | The temperature at which hot mechanical working of metal is completed. | ||||||||||||||||||||||||||||
Flange | (1) A projection of metal on formed objects. (2) The parts of a channel at right angles to the central section or web. | ||||||||||||||||||||||||||||
Flatness | Relative term for the measure of deviation of flat rolled material from a plane surface: usually determined as the height of ripples or waves above a horizontal level surface. | ||||||||||||||||||||||||||||
Fracture Test | Breaking a piece of metal for the purpose of examining the fractured surface to determine the structure or carbon content of the metal or to detect the presence of internal defects. | ||||||||||||||||||||||||||||
Full Annealing | A softening process in which a ferrous alloy is heated to a temperature above the transformation range and, after being held for a sufficient time at this temperature, is cooled slowly to a temperature below the transformation range. The alloy is ordinarily allowed to cool slowly in the furnace, although it may be removed and cooled in some medium that ensures a slow rate of cooling. | ||||||||||||||||||||||||||||
Grain Refiner | Any material added to a liquid metal for the purpose of producing a finer grain size in the subsequent casting, or of retaining fine grains during the heat treatment of wrought structures. | ||||||||||||||||||||||||||||
Grains | Individual crystals in metals. | ||||||||||||||||||||||||||||
Hardenability | In a ferrous alloy, the property that determines the depth and distribution of hardness induced by quenching. | ||||||||||||||||||||||||||||
Hardening | Any process for increasing the hardness of metal by suitable treatment, usually involving heating and cooling. | ||||||||||||||||||||||||||||
Hardness | Defined in terms of the method of measurement. (1) Usually the resistance to indentation. (2) Stiffness or temper of wrought products. (3) Machinability characteristics. |
||||||||||||||||||||||||||||
Heat Treatment | A combination of heating and cooling operations, timed and applied to a metal or alloy in the solid state in a way that will produce desired properties. Heating for the sole purpose of hot working is excluded from the meaning of this definition. | ||||||||||||||||||||||||||||
Homogeneous | Usually defined as having identical characteristics throughout. However, physical homogeneity may require only an identity of lattice type throughout, while chemical homogeneity requires uniform distribution of alloying elements. | ||||||||||||||||||||||||||||
Hot Forming | Working operations, such as bending and drawing sheet and plate, forging, pressing, and heading, performed on metal heated to temperatures above room temperature. | ||||||||||||||||||||||||||||
Hot Shortness | Brittleness in hot metal. | ||||||||||||||||||||||||||||
Hot Quenching | A process of quenching in a medium at a temperature substantially higher than atmospheric temperature. | ||||||||||||||||||||||||||||
Hot Working | Plastic deformation of metal at such a temperature and rate that strain hardening does not occur. The lower limit of temperature for this process is the recrystallization temperature. | ||||||||||||||||||||||||||||
Hydrogen Embrittlement | A condition of low ductility resulting from hydrogen absorption and internal pressure developed subsequently. | ||||||||||||||||||||||||||||
Impact Energy (Impact Value) | The amount of energy required to fracture a material, usually measured by means of an lzod or Charpy test. The type of specimen and testing conditions affect the values and therefore should be specified. | ||||||||||||||||||||||||||||
Impact Test | A test to determine the energy absorbed in fracturing a test bar at high velocity. The test may be in tension or in bending, or it may properly be a notch test if a notch is present, creating multiaxial stresses. | ||||||||||||||||||||||||||||
Incidental Elements | Small quantities of non-specified elements commonly introduced into product from the use of scrap metal with the raw materials. | ||||||||||||||||||||||||||||
Inclusions | Particles of impurities (usually oxides, sulfides, silicates and such) that are held mechanically, or are formed during solidification or by subsequent reaction within the solid metal. | ||||||||||||||||||||||||||||
Ingot | A casting intended for subsequent rolling or forging. | ||||||||||||||||||||||||||||
Iron | (1) Element No. 26 of the periodic system, the average atomic weight of the naturally occurring isotopes being 55.85. (2) Iron base materials not falling into the steel classifications. | ||||||||||||||||||||||||||||
Kaldo Process | One of the family of basic oxygen steelmaking processes which uses an inclined, rotating cylindrical furnace in which oxygen is injected through a lance in the center line of the furnace. This furnace uses a basic refractory lining and normally no fuels or fluxes are injected with the oxygen. | ||||||||||||||||||||||||||||
Killed Steel | Steel deoxidized with a strong deoxidizing agent such as silicon or aluminum in order to reduce the oxygen content to a minimum so that no reaction occurs between carbon and oxygen during solidification. | ||||||||||||||||||||||||||||
Ladle Analysis | Chemical analysis made from samples obtained during original casting ot ingots. This is normally the controlling analysis for satisfying the specification. | ||||||||||||||||||||||||||||
Laminations | Defects resulting from the presence of blisters, seams or foreign inclusions aligned parallel to the worked surface of a metal. | ||||||||||||||||||||||||||||
Lap | A surface defect appearing as a seam, caused by folding over hot metal, fins or sharp corners and then rolling or forging them into the surface, but not welding them. | ||||||||||||||||||||||||||||
L-0 Process | One of the basic oxygen steelmaking processes using a vertical cylindrical furnace in which oxygen is injected from above by a lance. The furnace has a basic refractory lining. Some variations of this process include the injection of liquid or gaseous fuels and fluxes along with the gaseous oxygen. | ||||||||||||||||||||||||||||
Longitudinal Direction | The direction in a wrought metal product parallel to the direction of working (drawing, extruding, rolling). | ||||||||||||||||||||||||||||
Lüder's Lines or Lüder Lines | (stretcher strains, flow figures) Elongated markings that appear on the surface of some materials, particularly iron and low-carbon steel, when deformed just past the yield point. These markings lie approximately parallel to the direction of maximum shear stress and are the result of localized yielding. They consist of depressions when produced in tension and of elevations when produced in compression. They may be made evident by localized roughening of a polished surface or by localized flaking from an oxidized surface. | ||||||||||||||||||||||||||||
Macroscopic | Visible either with the naked eye or under low magnification (as great as about 10 diameters). | ||||||||||||||||||||||||||||
Macrostructure | The structure of metals as revealed by macroscopic examination. | ||||||||||||||||||||||||||||
Malleability | The property that determines the ease of deforming a metal when the metal is subjected to rolling or hammering. The more malleable metals can be hammered or rolled into thin sheet more easily than others. | ||||||||||||||||||||||||||||
Mannesmann Process | A process used for piercing tube billets in making seamless tubing. The billet is rotated between two heavy rolls mounted at an angle, and is forced over a fixed mandrel. Billets are called "tube rounds". | ||||||||||||||||||||||||||||
Martensite | An unstable constituent in quenched steel, formed without diffusion and only during cooling below a certain temperature known as the M 5 (or Ar") temperature. The structure is characterized by its acicular appearance on the surface of a polished and etched specimen. Martensite is the hardest of the transformation products of austenite. Tetragonality of the crystal structure is observed when the carbon content is greater than about 0.5% | ||||||||||||||||||||||||||||
Mechanical Properties | Those properties of a material that reveal the elastic and inelastic reaction when force is applied, or that involve the relationship between stress and strain; for example, the modulus of elasticity, tensile strength and fatigue limit. These properties have often been designated as "physical properties", but the term "mechanical properties" is preferred. | ||||||||||||||||||||||||||||
Mechanical Working | Subjecting metal to pressure exerted by rolls, dies, presses, or hammers, to change its form or to affect the structure and consequently the mechanical and physical properties. | ||||||||||||||||||||||||||||
Merchant Mill | A mill, consisting of a group of stands of three rolls each arranged in a straight line and driven by one power unit, used to roll rounds, squares or flats of smaller dimensions than would be rolled on the bar mill. | ||||||||||||||||||||||||||||
Microstructure | The structure of polished and etched metal and alloy specimens as revealed by the microscope. | ||||||||||||||||||||||||||||
Modulus of Elasticity | The slope of the elastic portion of the stress-strain curve in mechanical testing, The stress is divided by the unit elongation. The tensile or compressive elastic modulus is called "Young's modulus"; the torsional elastic modulus is known as the "shear modulus", or "modulus of rigidity". | ||||||||||||||||||||||||||||
Normalizing | A process in which a ferrous alloy is heated to a suitable temperature above the transformation range and is subsequently cooled in still air at room temperature. | ||||||||||||||||||||||||||||
Normal Segregation | Concentration of alloying constituents that have low melting points, in those portions of a casting that solidify last. | ||||||||||||||||||||||||||||
Notch Brittleness | Susceptibility of a material to brittleness in areas containing a groove, scratch, sharp fillet or notch. | ||||||||||||||||||||||||||||
Notch Sensitivity | The reduction caused in nominal strength, impact or static, by the presence of a stress concentration, usually expressed as the ratio of the notched to the un-notched strength. | ||||||||||||||||||||||||||||
Open Hearth Furnace | A furnace for melting metal, in which the bath is heated by the convection of hot gases over the surface of the metal and by radiation from the roof. | ||||||||||||||||||||||||||||
Out-of-Round | Deviation of cross section of a round bar from a true circle: normally measured as difference between maximum and mini-mum diameters at the same cross section of the bar. | ||||||||||||||||||||||||||||
Out-of-Square | For square bars this is the deviation of cross section from a true square: normally measured as the difference between the two diagonal dimensions at one cross section. For structural shapes, the term out-of-square indicates the deviation from a right angle of the plane of flanges in relation to the plane of webs. |
||||||||||||||||||||||||||||
Overheated | A term applied when, after exposure to an excessively high temperature, a metal develops an undesirably coarse grain structure but is not permanently damaged. Unlike a burnt structure, the structure produced by overheating can be corrected by suitable heat treatment, by mechanical work, or by a combination of the two. | ||||||||||||||||||||||||||||
Pearlite | The lamellar aggregate of ferrite and carbide. NOTE: It is recommended that this word be reserved for the microstructures consisting of thin plates or lamellae that is, those that may have a pearly luster in white light. The lamellae can be very thin and resolvable only with the best microscopic equipment and technique. |
||||||||||||||||||||||||||||
Physical Properties | Those properties familiarly discussed in physics, exclusive of those described under mechanical properties; for example, density, electrical conductivity, coefficient of thermal expansion. This term has often been used to describe mechanical properties but this usage is not recommended. See mechanical properties. | ||||||||||||||||||||||||||||
Pickle | Chemical or electrochemical removal of surface oxides. | ||||||||||||||||||||||||||||
Pig Iron | Iron produced by reduction of iron ore in the blast furnace. | ||||||||||||||||||||||||||||
Pipe | A cavity formed by contraction in metal (especially ingots) during solidification of the last portion of liquid metal. | ||||||||||||||||||||||||||||
Pit | A sharp depression in the surface of metal. | ||||||||||||||||||||||||||||
Plastic Deformation | Permanent distortion of a material under the action of applied stresses. | ||||||||||||||||||||||||||||
Plasticity | The ability of a metal to be deformed extensively without rupture. | ||||||||||||||||||||||||||||
Poisson's Ratio | The absolute value of the ratio of the transverse strain to the corresponding axial strain, in a body subjected to uniaxial stress; usually applied to elastic conditions. | ||||||||||||||||||||||||||||
Porosity | Unsoundness caused in cast metals by the presence of blowholes and shrinkage cavities. | ||||||||||||||||||||||||||||
Primary Mill | A mill for rolling ingots or the rolled products of ingots to blooms, billets or slabs. This type of mill is often called a blooming mill and sometimes a cogging mill. | ||||||||||||||||||||||||||||
Proof Stress | In a test, stress that will cause a specified permanent deformation in a material, usually 0.01% or less. | ||||||||||||||||||||||||||||
Proportional limit | The greatest stress that the material is capable of sustaining without a deviation from the law of proportionality of stress to strain (Hooke's Law). | ||||||||||||||||||||||||||||
Quenching | A process of rapid cooling from an elevated temperature by contact with liquids, gases or solids. | ||||||||||||||||||||||||||||
Quenching Crack | A fracture resulting from thermal stresses induced during rapid cooling or quenching: frequently encountered in alloys that have been overheated and liquated and are thus "hot short". | ||||||||||||||||||||||||||||
Recrystallization | A process whereby the distorted grain structure of cold worked metals is replaced by a new, strain-free grain structure during annealing above a specific minimum temperature. | ||||||||||||||||||||||||||||
Red Shortness | Brittleness in steel when it is red hot. | ||||||||||||||||||||||||||||
Reduction in Area | The difference between the original cross-sectional area and that of the smallest area at the point of rupture; usually stated as a percentage of the original area; also called "contraction of area". | ||||||||||||||||||||||||||||
Refining Temperature | A temperature, usually just higher than the transformation range, employed in the heat treatment of steel to refine the structure in particular, the grain size. | ||||||||||||||||||||||||||||
Residual Stress | Macroscopic stresses that are set up within a metal as the result of non-uniform plastic deformation. This deformation may be caused by cold working or by drastic gradients of temperature from quenching or welding. | ||||||||||||||||||||||||||||
Resquared | Flat rolled material (plate, sheet or strip) firstly cut to approximate size and finally re-sheared to very close tolerances: also any material having been cut to equally close tolerances as to dimensions and squareness, by whatever method. | ||||||||||||||||||||||||||||
Reverberatory Furnace | A furnace with a shallow hearth, usually non-regenerative, having a roof that deflects the flame and radiates heat toward the hearth or the surface of the charge. | ||||||||||||||||||||||||||||
Rimmed Steel | An incompletely deoxidized steel normally containing less than 0.25% C and having the following characteristics: (a) During solidification an evolution of gas occurs sufficient to maintain a liquid ingot top ("open" steel) until a side and bottom rim of substantial thickness has formed. If the rimming action is intentionally stopped shortly after the mould is filled, the product is termed capped steel. (b) After complete solidification, the ingot consists of two distinct zones-a rim somewhat purer than when poured and a core containing scattered blowholes, a minimum amount of pipe and an average percentage of metalloids somewhat higher than when poured and markedly higher in the upper portion of the ingot. | ||||||||||||||||||||||||||||
Rockwell Hardness Test | A test for determining the hardness of a material based upon the depth of penetration of a specified penetrator into the specimen under certain arbitrarily fixed conditions of test. | ||||||||||||||||||||||||||||
Roller Flattening or Roller Levelling | The process in which a series of staggered rolls of small diameter is used to remove bow and waves from sheet. While passing through the rolls, the sheet is bent back and forth slightly and is delivered approximately flat. | ||||||||||||||||||||||||||||
Roller Straightening | A process involving a series of staggered rolls of small diameter, between which rod, tubing and shapes are passed for the purpose of straightening. The process consists of a series of bending operations. | ||||||||||||||||||||||||||||
Roll Forming | (1) An operation used in forming sheet. Strips of sheet are passed between rolls of definite settings that bend the sheet progressively into structural members of various contours, sometimes called "moulded sections". (2) A process of coiling sheet into open cylinders. |
||||||||||||||||||||||||||||
Rolling | Reducing the cross-sectional area of metal stock, or otherwise shaping metal products, through the use of rotating rolls. | ||||||||||||||||||||||||||||
Rolling Mills | Machines used to decrease the cross-sectional area of metal stock and produce certain desired shapes as the metal passes between rotating rolls mounted in a framework comprising a basic unit called a stand. Cylindrical rolls produce flat shapes; grooved rolls produce rounds, squares and structural shapes. Among rolling mills may be listed the billet mill, blooming mill, breakdown mill, plate mill, sheet mill, slabbing mill, strip mill and temper mill. | ||||||||||||||||||||||||||||
Scab | (scabby) A blemish caused on a casting by eruption of gas from the mould face, or by uneven mould surfaces; or occurring where the skin from a blowhole has partly burned away and is not welded. | ||||||||||||||||||||||||||||
Scaling | Surface oxidation caused on metals by heating in air or in other oxidizing atmospheres. | ||||||||||||||||||||||||||||
Scarfing | Cutting surface areas of metal objects, ordinarily by using a gas torch. The operation permits surface defects to be cut from ingots, billets, or the edges of plate that is to be bevelled for butt welding. See chipping. | ||||||||||||||||||||||||||||
Seam | On the surface of metal. a crack that has been closed but not welded; usually produced by some defect either in casting or in working, such as blowholes that have become oxidized or folds and laps that have been formed during working. Seam also refers to lap joints, as in seam welding. | ||||||||||||||||||||||||||||
Segregation | In an alloy object, concentration of alloying elements at specific regions, usually as a result of the primary crystallization of one phase with the subsequent concentration of other elements in the remaining liquid. Micro-segregation refers to normal segregation on a microscopic scale whereby material richer in alloying element freezes in successive layers on the dendrites (coring) and in the constituent network. Macro-segregation refers to gross differences in concentration (for example, from one area of an ingot to another) which may be normal, inverse or gravity segregation. | ||||||||||||||||||||||||||||
Semi-killed Steel | Steel incompletely deoxidized, to permit evolution of sufficient carbon monoxide to offset solidification shrinkage. | ||||||||||||||||||||||||||||
Sheared Edges | Sheared edge is obtained when rolled edge is removed by rotary slitter or mechanical shear. | ||||||||||||||||||||||||||||
Shortness | A form of brittleness in metal. It is designated as "cold", "hot", and "red” to indicate the temperature range in which the brittleness occurs. | ||||||||||||||||||||||||||||
Single-Stand Mill | A rolling mill of such design that the product contacts only two rolls at a given moment. Contrast with “tandem mill”. | ||||||||||||||||||||||||||||
Sinkhead or Hot Top | A reservoir insulated to retain heat and to hold excess molten metal on top of an ingot mold, in order to feed the shrinkage of the ingot. Also called "shrink head" or "feeder head". | ||||||||||||||||||||||||||||
Skelp | A plate of steel or wrought iron from which pipe or tubing is made by rolling the skelp into shape longitudinally and welding the edges together. | ||||||||||||||||||||||||||||
Skin | A thin surface layer that is different from the main mass of a metal object, in composition, structure or other characteristics. | ||||||||||||||||||||||||||||
Slab | See bloom. | ||||||||||||||||||||||||||||
Slag | A nonmetallic product resulting from the mutual dissolution of flux and nonmetallic impurities in smelting and refining operations. | ||||||||||||||||||||||||||||
Soaking Spheroidizing | Prolonged heating of a metal at a selected temperature. Any process of heating and cooling that produces a rounded or globular form of carbide in steel spheroidizing methods frequently used are: 1. Prolonged holding at a temperature just below Ae1 2. Heating and cooling alternately between temperatures that are just above and just below Ae1 . 3. Heating to a temperature above Ae1 or Ae3 and then cooling very slowly in the furnace, or holding at a temperature just below Ae1. 4. Cooling at a suitable rate from the minimum temperature at which all carbide is dissolved, to prevent the re-formation of a carbide network, and then reheating in accordance with method 1 or 2 above (applicable to hypereutectoid steel containing a carbide network). |
||||||||||||||||||||||||||||
Steel | An iron base alloy, malleable in some temperature range as initially cast, containing manganese, usually carbon, and often other alloying elements. In carbon steel and low-alloy steel, the maximum carbon is about .20%; in high-alloy steel, about .25%. The dividing line between low-alloy and high-alloy steels is generally regarded as being about 5% metallic alloying elements. Steel is to be differentiated from two general classes of "irons": the cast irons, on the high-carbon side, and the relatively pure irons such as ingot iron, carbonyl iron, and electrolytic iron, on the low-carbon side. In some steels containing extremely low carbon, the manganese content is the principal differentiating factor, steel usually containing at least 0.25%; ingot iron contains considerably less. | ||||||||||||||||||||||||||||
Straightness | Measure of adherence to or deviation from a straight line, normally expressed as sweep or camber, according to the plane. | ||||||||||||||||||||||||||||
Strain Aging | Aging induced by cold working. See aging. | ||||||||||||||||||||||||||||
Strain Energy | (1) The work done in deforming a body. 121 The work done in deforming a body within the elastic limit of the material. It is more properly elastic strain energy and can be recovered as work rather than heat. | ||||||||||||||||||||||||||||
Strain Hardening | An increase in hardness and strength caused by plastic deformation at temperatures lower than the recrystallization range. | ||||||||||||||||||||||||||||
Stress | The load per unit of area. Ordinarily stress-strain curves do not show the true stress (load divided by area at that moment) but a fictitious value obtained by using always the original area. | ||||||||||||||||||||||||||||
Stress-Corrosion Cracking | Failure by cracking under combined action of corrosion and stress, either external (applied) or internal (residual). Cracking may be either intergranular or transgranular, depending on metal and corrosive medium. | ||||||||||||||||||||||||||||
Stress Raisers | Factors such as sharp changes in contour or surface defects, which concentrate stresses locally. | ||||||||||||||||||||||||||||
Stress Relieving | A process of reducing residual stresses in a metal object by heating the object to a suitable temperature and holding for a sufficient time. This treatment may be applied to relieve stresses induced by casting, quenching, normalizing, machining, cold working, or welding. | ||||||||||||||||||||||||||||
Stretcher Flattening or Stretcher levelling | A process for removing bow and warpage from sheet by applying a uniform tension at the ends so that the piece is elongated to a definite amount of permanent set. | ||||||||||||||||||||||||||||
Stretcher levelled Flatness | Steel sheets or strip subjected to stretcher levelling thereby acquire a high degree of flatness, (together with some increase of stiffness). When the same degree of flatness is procured by other methods like roller levelling, it is then described as "stretcher levelled standard of flatness". | ||||||||||||||||||||||||||||
Stretcher Strains | See "Lüder lines". | ||||||||||||||||||||||||||||
Sweep | Curvature in structural and other similar shapes normal to the plane of the web. | ||||||||||||||||||||||||||||
Tandem Mill | A rolling mill consisting of two or more stands arranged so that the metal being processed travels in a straight line from stand to stand. In continuous rolling, the various stands are synchronized so that the strip may be rolled in all stands simultaneously. Contrast with "single-stand mill". | ||||||||||||||||||||||||||||
Tempering | A process of reheating quench-hardened or normalized steel to a temperature below the transformation range, and then cooling at any rate desired. | ||||||||||||||||||||||||||||
'Temper' Brittleness | Brittleness that results when certain steels are held within, or are cooled slowly through, a certain range of temperature below the transformation range. The brittleness is revealed by notched-bar impact tests at room temperature or lower temperatures. | ||||||||||||||||||||||||||||
Tensile Strength | The value obtained by dividing the maximum load observed during tensile straining by the specimen cross-sectional area before straining. Also called "ultimate strength". | ||||||||||||||||||||||||||||
Thermal Fatigue | Fracture resulting from the presence of temperature gradients which vary with time in such a manner as to produce cyclic stresses in a structure. | ||||||||||||||||||||||||||||
Tolerances | Allowable variations from specified dimensions. | ||||||||||||||||||||||||||||
Toughness | Property of absorbing considerable energy before fracture; usually represented by the area under a stress-strain curve, and therefore involving both ductility and strength. | ||||||||||||||||||||||||||||
Trace | Extremely small quantity of an element, usually too small to determine quantitatively. | ||||||||||||||||||||||||||||
Transformation Range or Transformation Temperature Range | The temperature interval within which austenite forms while ferrous alloys are being heated. Also the temperature interval within which austenite disappears while ferrous alloys are being cooled. The two ranges are distinct, sometimes overlapping but never coinciding. The limiting temperatures of the ranges depend on the composition of the alloy and on the rate of change of temperature, particularly during cooling. See transformation temperature. | ||||||||||||||||||||||||||||
Transformation Temperature | The temperature at which a change in phase occurs. The term is sometimes used to denote the limiting temperature of a trans-formation range. The following symbols are used for iron and steel:
NOTE: All these changes (except the formation of martensite) occur at lower temperatures during cooling than during heating, and depend on the rate of change of temperature. The temperatures of phase changes at equilibrium are denoted by the symbols Ae1 Ae3 AeCM and Ae4 . |
||||||||||||||||||||||||||||
Transverse | Literally “across" signifying a direction or plane perpendicular to the direction of working. | ||||||||||||||||||||||||||||
Ultimate Strength | See tensile strength. | ||||||||||||||||||||||||||||
Universal Mill | A rolling mill in which rolls with a vertical axis roll the edges of the metal stock between some of the passes through the horizontal rolls. | ||||||||||||||||||||||||||||
Universal Mill Plate | Plate rolled on a universal mill having vertical (edge) rolls as well as horizontal rolls; also any plate having characteristics identical to plate produced on a universal mill. | ||||||||||||||||||||||||||||
Upsetting | (1) A metal working operation similar to forging. (2) The process of axial flow under axial compression of metal, as in forming heads on rivets by flattening the end of wire. |
||||||||||||||||||||||||||||
Welding | A process used to join metals by the application of heat. Fusion welding, which includes gas, arc, and resistance welding, requires that the parent metals be melted. This distinguishes fusion welding from brazing. In pressure welding joining is accomplished by the use of heat and pressure without melting. The parts that are being welded are pressed together and heated simultaneously, so that recrystallization occurs across the interface. | ||||||||||||||||||||||||||||
Woody Fracture | Fractures having a fibrous appearance. | ||||||||||||||||||||||||||||
Yield Point | In mild or medium-carbon steel. the stress at which a marked increase in deformation occurs without increase in load. In other steels, and in nonferrous metals this phenomenon is not observed. See Yield Strength. | ||||||||||||||||||||||||||||
Yield Strength | The stress at which a material exhibits a specified limiting deviation from proportionality of stress to strain. An offset of 0.2% is used for many metals such as aluminum-base and magnesium-base alloys, while a 0.5% total elongation under load is frequently used for copper alloys. | ||||||||||||||||||||||||||||
Young's Modulus | The modulus of elasticity in tension or compression. |